Inhaltsverzeichnis:
- Erkennung und Gestaltung von Hinterschnitten bei Kunststoff-Spritzgussteilen
- Verständnis von Hinterschnitten bei Kunststoff-Spritzgussteilen
- Methoden Zur Erkennung Von Hinterschnitten Im Bauteildesign
- Gestaltungsprinzipien Zur Vermeidung Von Hinterschnitten
- Techniken Zur Umsetzung Von Hinterschnitten Im Spritzguss
- Einfluss von Hinterschnitten auf Werkzeugkosten und Fertigungszeit
- Best Practices und Tipps für Designer und Ingenieure
- Abschluss
Im Bereich der Kunststoffverarbeitung stellen Hinterschnitte eine erhebliche Herausforderung dar. Sie beeinflussen sowohl die Gestaltung als auch die Funktionalität von Spritzgussteilen. Doch wie erkennt man Hinterschnitte im Designprozess und welche Möglichkeiten es gibt, diese in der Fertigung zu berücksichtigen, ohne die Dichte und Qualität zu mindern? Dieser Artikel beleuchtet Methoden zur Identifikation und Gestaltungsprinzipien, die helfen, Hinterschnitte effektiv zu handhaben. Zudem zeigt er auf, wie der Einsatz moderner Technologien wie 3D-Druck den Werkzeugbau revolutionieren kann, um so die Herstellungskosten zu optimieren und die Produktionszeiten zu verkürzen. Leser werden von praxisnahen Tipps profitieren, die direkt auf die Bedürfnisse und Herausforderungen von Ingenieuren und CEOs abgestimmt sind.
Verständnis Von Hinterschnitten Bei
Kunststoff
-Spritzgussteile
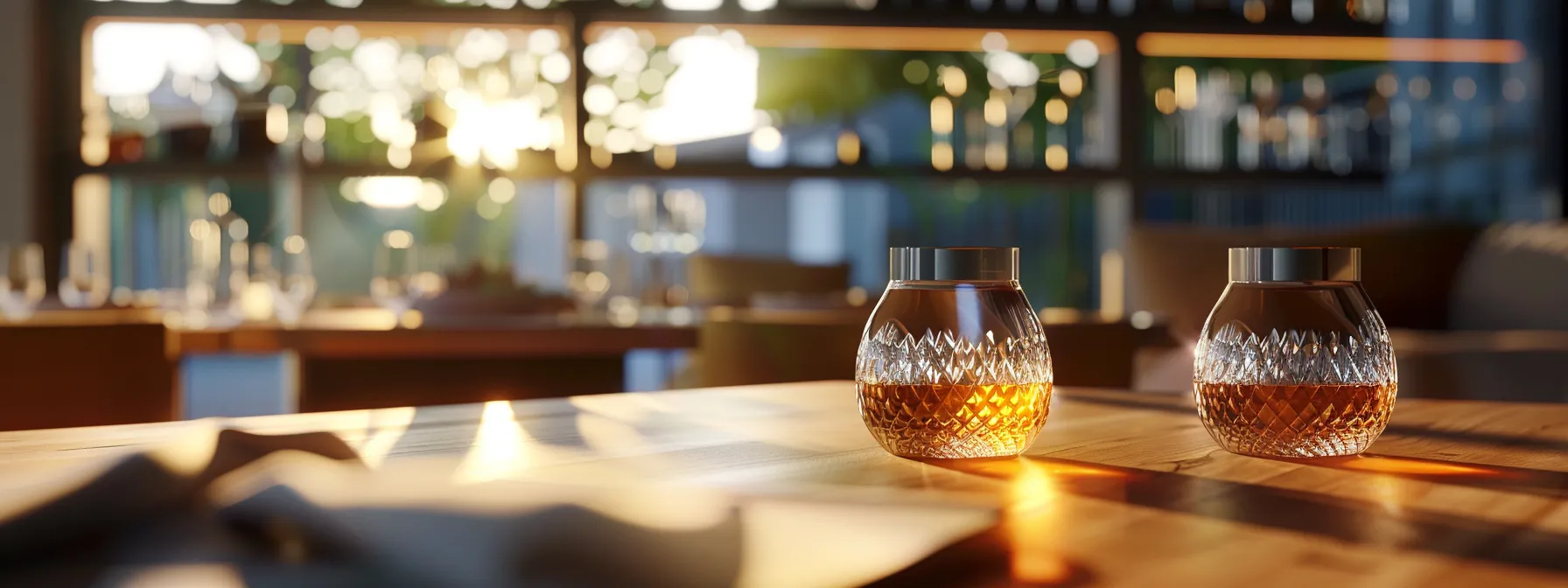
Die Gestaltung von Hinterschnitten bei Kunststoffspritzgussteilen ist ein kritischer Aspekt für Ingenieure und Designer. Ein Verständnis für die Definition und Bedeutung von Hinterschnitten, typische Beispiele in der Praxis, sowie die Auswirkungen auf den Spritzgussprozess sind entscheidend. Dieses Wissen beeinflusst maßgeblich die Bohrungen, Kosten, die Durchbiegung einzelner Komponenten und das Design der Verpackung. Im Folgenden werden diese Themen detailliert besprochen, um einen klaren Überblick über die Komplexitäten zu geben, die mit Hinterschnitten verbunden sind.
Definition Und Bedeutung Von Hinterschnitten
In der Kunststoffindustrie bezeichnet der Begriff Faserverstärkte Kunststoffteile Hinterschnitte Elemente in Spritzgussteilen, die eine normale Entformung behindern würden. Sie sind von grundlegender Bedeutung für die Integration komplexer Funktionen in Bauteilen, beispielsweise zur Unterbringung von Elektronik oder für Sicherheitsschlösser. Die richtige Gestaltung der Hinterschnitte berücksichtigt Faktoren wie Toleranz und Viskosität des Kunststoffs und stellt daher hohe Anforderungen an die Präzision im Spritzgussprozess.
Ohne eine exakte Konstruktion und ein durchdachtes Schleifen der entsprechenden Werkzeugteile können Hinterschnitte zu einem erhöhten Risiko von Beschädigungen an den Bauteilen führen. Dies beeinflusst nicht nur die Funktionalität sondern kann auch zusätzliche Kosten verursachen. Deshalb ist ein fundiertes Verständnis der Gestaltung von Hinterschnitten unerlässlich, um die Effizienz und Qualität in der Produktion von Kunststoffteilen sicherzustellen.
Typische Beispiele in Der Praxis
Im Bereich des Spritzgießens sind Rippendesigns ein klassisches Beispiel für Hinterschnitte, die sowohl die strukturelle Integrität stärken als auch die Wärmeleitfähigkeit optimieren. Diese Elemente müssen präzise gestaltet werden, um ihre Funktion ohne negative Auswirkungen auf die Massenproduktion zu erfüllen. Solche Herausforderungen im Formenbau erfordern ein tiefgehendes Verständnis von Materialeigenschaften und Spritzgießtechniken.
Ein weiteres Praxisbeispiel ist die Integration innerer und äußerer Hinterschnitte für Verbindungsmechanismen, die in verschiedensten Anwendungen von Automotive bis zur Unterhaltungselektronik genutzt werden. Gerade diese Komponenten weisen auf, wie kritische Aspekte wie Materialauswahl und Design des Spritzgießwerkzeugs den gesamten Herstellungsprozess beeinflussen und letztendlich die Effizienz der Massenproduktion bestimmen.
Auswirkungen Auf Den Spritzgussprozess
Die Gestaltung von Hinterschnitten kann den Volumenstrom des Kunststoffs während des Spritzgussprozesses wesentlich beeinflussen. Wird beispielsweise Werkzeugstahl bei der Herstellung der Formen nicht korrekt bearbeitet, kann dies zu turbulenten Strömungen führen, welche die Füllung der Form erschweren und die Eigenschaften des endgültigen Produkts aus Polyethylen oder anderem Material beeinträchtigen.
Zudem erhöht die Komplexität von Hinterschnitten den Wartungsaufwand von Spritzgusswerkzeugen. Unregelmäßige Wartungen oder unzureichend berücksichtigte Hinterschnitte können zu vorzeitigem Verschleiß führen und somit zu erhöhten Stillstandzeiten der Produktionsanlagen, was letztlich die Kosten und die Effizienz der Produktion negativ beeinflusst.
Methoden Zur Erkennung Von Hinterschnitten Im Bauteildesign
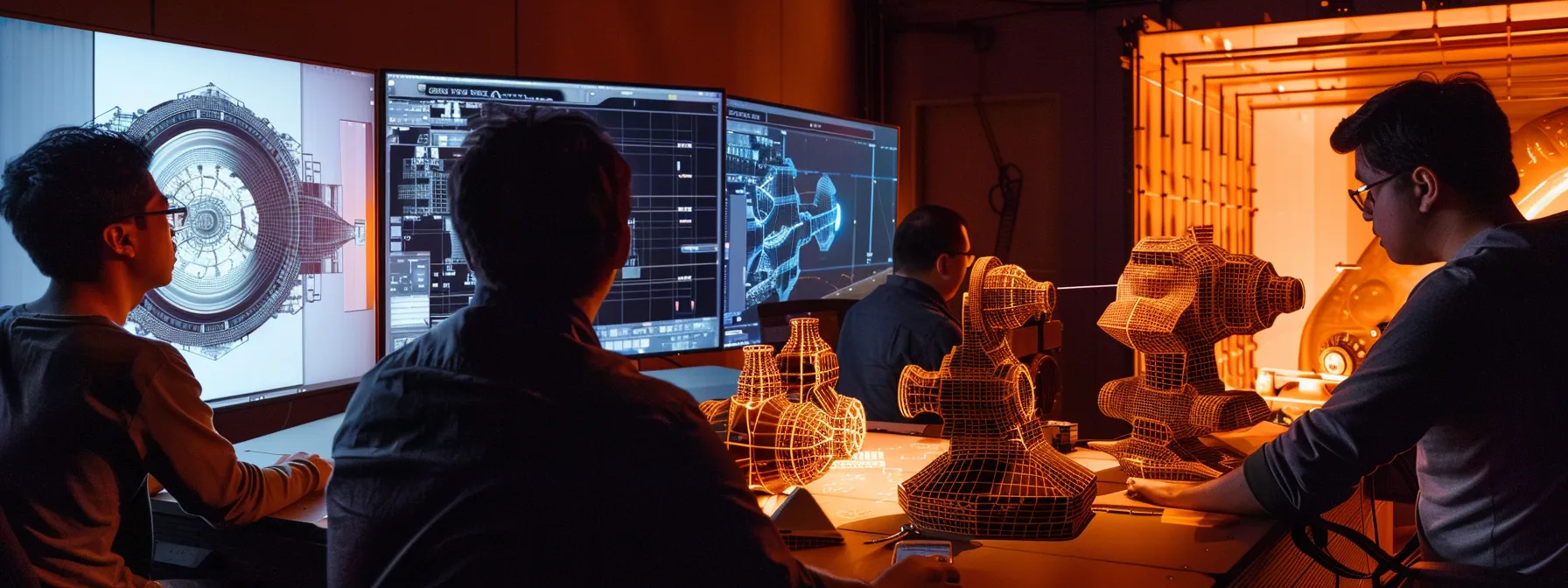
Die Identifizierung von Hinterschnitten in der Konstruktion von Kunststoff-Spritzgussteilen ist essentiell für die Qualität und Machbarkeit des Endprodukts. Insbesondere die Analyse von 3D-CAD-Modellen bietet tiefgehende Einblicke in die Konstruktionseigenschaften von Thermoplasten wie Polystyrol. Der Einsatz von Spritzgusssimulationssoftware ermöglicht darüber hinaus die Vorhersage des Materialverhaltens und die Optimierung des Radius an kritischen Stellen. Durch die Automatisierung dieser Prozesse und die enge Zusammenarbeit mit Werkzeugbauern lassen sich Hinterschnitte frühzeitig erkennen und effiziente Lösungen entwickeln.
Analyse Von 3d-Cad-Modellen
Die Nutzung fortschrittlicher 3D-CAD-Modelle spielt eine entscheidende Rolle bei der Identifizierung und Analyse von Hinterschnitten in Spritzgussteilen. Durch diese Modelle können Ingenieure die Gestaltung komplexer Geometrien, wie die von thermoplastischen Elastomeren, virtuell simulieren und potenzielle Schwachstellen, beispielsweise im Hinblick auf die Zugfestigkeit der Materialien, präzise ausfindig machen.
Darüber hinaus erlauben diese Modelle eine detaillierte Planung des Polierprozesses von Werkzeugoberflächen, was für die Herstellung von Qualitätsprodukten auf der Maschine unabdingbar ist. Metallkomponenten im Werkzeugbau, die aufgrund ihrer Geometrie Schwierigkeiten beim Entformen bereiten könnten, lassen sich so optimieren, dass ein reibungsloser Produktionsablauf gewährleistet ist.
Einsatz Von Spritzgusssimulationssoftware
Der Einsatz von Spritzgusssimulationssoftware ist ein unerlässliches Werkzeug zur Prüfung und Optimierung von Kunststoffteilen hinsichtlich ihrer Fertigungsqualität. Mittels präziser Simulation wird der Schmelzpunkt des Materials virtuell replicated, um Einflussfaktoren wie Kühlung, Temperatur und ästhetische Eigenschaften wie die Passung zu untersuchen. So erlangen Ingenieure wichtige Erkenntnisse über das Verhalten der Schmelze in der Form und mögliche Designanpassungen, bevor das Teil in die Produktion geht.
Die Software ermöglicht eine realitätsnahe Abbildung des Spritzgießprozesses und hilft dabei, Komplikationen, die durch komplexe Hinterschnitte entstehen, zu minimieren. Durch Anpassung der Parameter für Temperatur und Kühlung können Ingenieure sicherstellen, dass die ästhetische Qualität und die Genauigkeit der Passung der Spritzgussteile, selbst bei schwierigen Hinterschnitten, gewährleistet ist. Dies trägt maßgeblich dazu bei, die Effektivität des Formenbaus zu steigern und die Zeit bis zur Markteinführung zu verkürzen.
Zusammenarbeit Mit Werkzeugbauern
Die Kooperation mit erfahrenen Werkzeugbauern spielt eine entscheidende Rolle, um die Hinterschnitte bei Kunststoff-Spritzgussteilen richtig zu identifizieren und zu gestalten. Insbesondere bei komplexen Geometrien ist deren Expertise gefragt, um sicherzustellen, dass Materialien wie Polyurethane beim Vakuumgießen gleichmäßig erstarren und die Hitzebeständigkeit gewährleistet ist. Eine enge Abstimmung ermöglicht die Umsetzung von präzisen und kosteneffektiven Werkzeugen für den Spritzgussprozess.
Ein tiefgreifendes Verständnis für die Gestaltung von Spritzgussformen, das Werkzeugbauer mitbringen, trägt wesentlich zur Optimierung von Produktionsabläufen bei. Bereits in der Entwurfsphase werden durch Simulationen und Beratung kritische Punkte wie Hinterschnitte erkannt und durch Anpassungen in der Geometrie des Werkzeugs berücksichtigt. So wird vermieden, dass Teile durch Überschuss an Material oder unzureichende Kühlung fehlerhaft erstarren, was zur Effizienzsteigerung und Reduzierung von Ausschussraten führt.
Gestaltungsprinzipien Zur Vermeidung Von Hinterschnitten
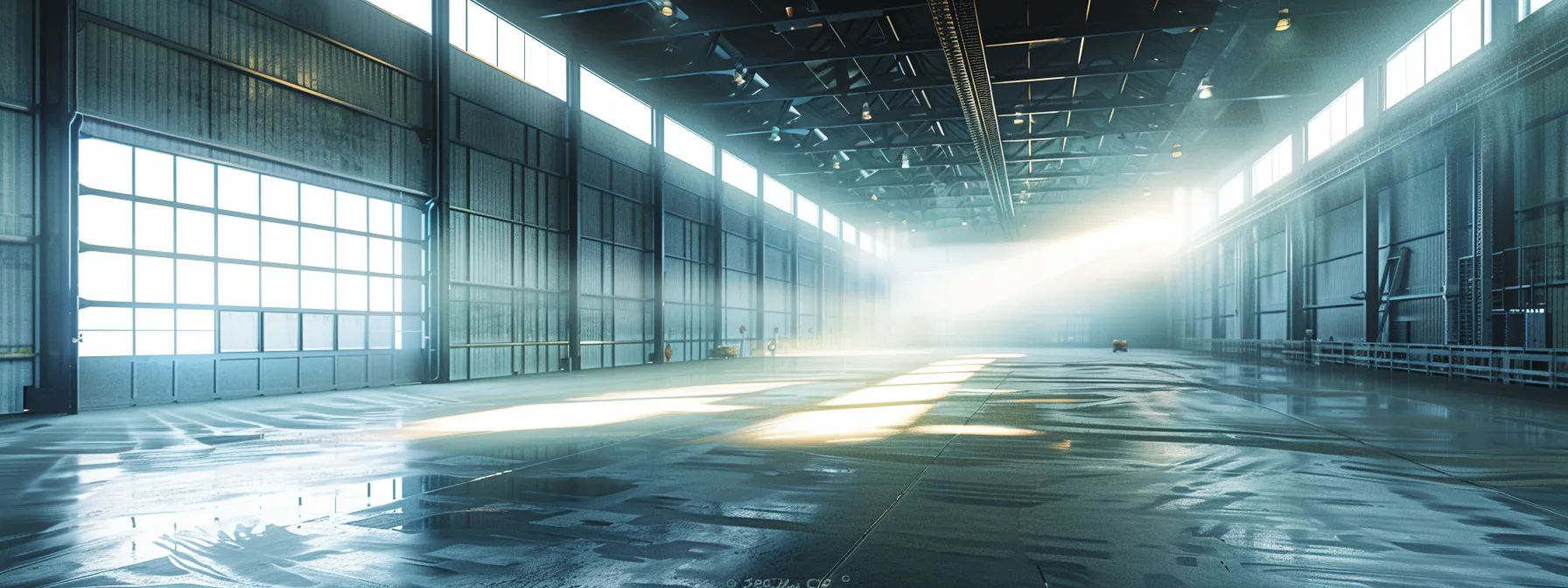
Die ausgeklügelte Gestaltung von Kunststoff-Spritzgussteilen verlangt nicht nur ein tiefes Verständnis für den Einsatz von geeigneten Entformungsschrägen, sondern ebenso für die Optimierung der Teilegeometrie und das Auffinden von Alternativen zu Hinterschnitten. Steifigkeit, Qualitätssicherung, sowie das Gießen hochwertiger Polymere hängen maßgeblich von der formschrägen Gestaltung ab. Im Folgenden werden die Prinzipien zur Vermeidung von Hinterschnitten dargelegt, die entscheidend für die Funktionalität und Wirtschaftlichkeit im Kunststoff-Spritzguss sind.
Einsatz Von Geeigneten Entformungsschrägen
Die Berücksichtigung von Wärmeausdehnung ist essentiell beim Einsatz von geeigneten Entformungsschrägen in der Kunststoff-Spritzgussfertigung. Insbesondere bei der Verarbeitung von Materialien wie Polyvinylchlorid (PVC) oder Polypropylen wirkt sich die thermische Expansion auf Verformung und Maßhaltigkeit der Teile aus. Eine präzise Berechnung der Entformungsschrägen trägt dazu bei, dass die Teile trotz Wärmeveränderungen ihre Form beibehalten und leicht aus der Form gelöst werden können.
Die Verwendung von Polybutylenterephthalat (PBT) in Präzisionsteilen erfordert eine akkurate Gestaltung der Entformungsschrägen, um eine optimale Verarbeitung und Verformung des Materials sicherzustellen. Durch eine angepasste Schräge wird die Gefahr von Beschädigungen reduziert und die Lebensdauer des Spritzgusswerkzeugs verlängert, was sich positiv auf die Produktionseffizienz und die Qualität der Spritzgussteile auswirkt.
Optimierung Der Teilegeometrie
Die Optimierung der Teilegeometrie ist ein entscheidender Schritt, um Hinterschnitte bei Kunststoff-Spritzgussteilen zu minimieren. Durch geschicktes Design und den Einsatz modernster CAD-Software können Konstrukteure Bauteile so gestalten, dass aufwendige Bearbeitungen wie Machining reduziert und Klebeverfahren zur Befestigung von zusätzlichen Komponenten vermieden werden. Diese Vorgehensweise trägt nicht nur dazu bei, die Schlagzähigkeit des Endprodukts zu verbessern, sondern ermöglicht auch eine höhere Geschwindigkeit in der Produktion.
Darüber hinaus fördert die intelligente Anordnung von Bauteilgeometrien die Innovation in der Fertigungstechnologie von Kunststoff-Spritzgussteilen. Die Reduktion von Hinterschnitten durch anspruchsvolle Geometrieoptimierungen spiegelt sich in einer verbesserten Produkthaltbarkeit und vereinfachten Montageprozessen wider. Somit stellen präzise und bedachte Designänderungen einen zentralen Faktor für die Effizienzsteigerung und Kostensenkung in der Kunststoffverarbeitung dar.
Alternativen Zu Hinterschnitten Finden
Die Implementierung von Rapid Prototyping Techniken bietet eine effektive Strategie, um Alternativen zu Hinterschnitten in der Gestaltung von Kunststoff-Spritzgussteilen zu finden. Unter anderem ermöglicht es die Herstellung von Prototypen aus Polyethylenterephthalat, um die Machbarkeit verschiedener Designs ohne Hinterschnitte zu testen und die Textur sowie Festigkeit dieser Alternativen praxisnah zu evaluieren.
Innovative Technik und präzises Engineering können bei Kunststoff-Spritzgussteilen die Notwendigkeit von Hinterschnitten reduzieren. Beispielsweise kann eine angepasste Textur der Oberfläche dazu beitragen, die Entformbarkeit zu verbessern, ohne auf Hinterschnitte zurückgreifen zu müssen, was sowohl die Implementierung in die Produktion vereinfacht als auch die Gesamtkosten senkt.
Techniken Zur Umsetzung Von Hinterschnitten Im Spritzguss
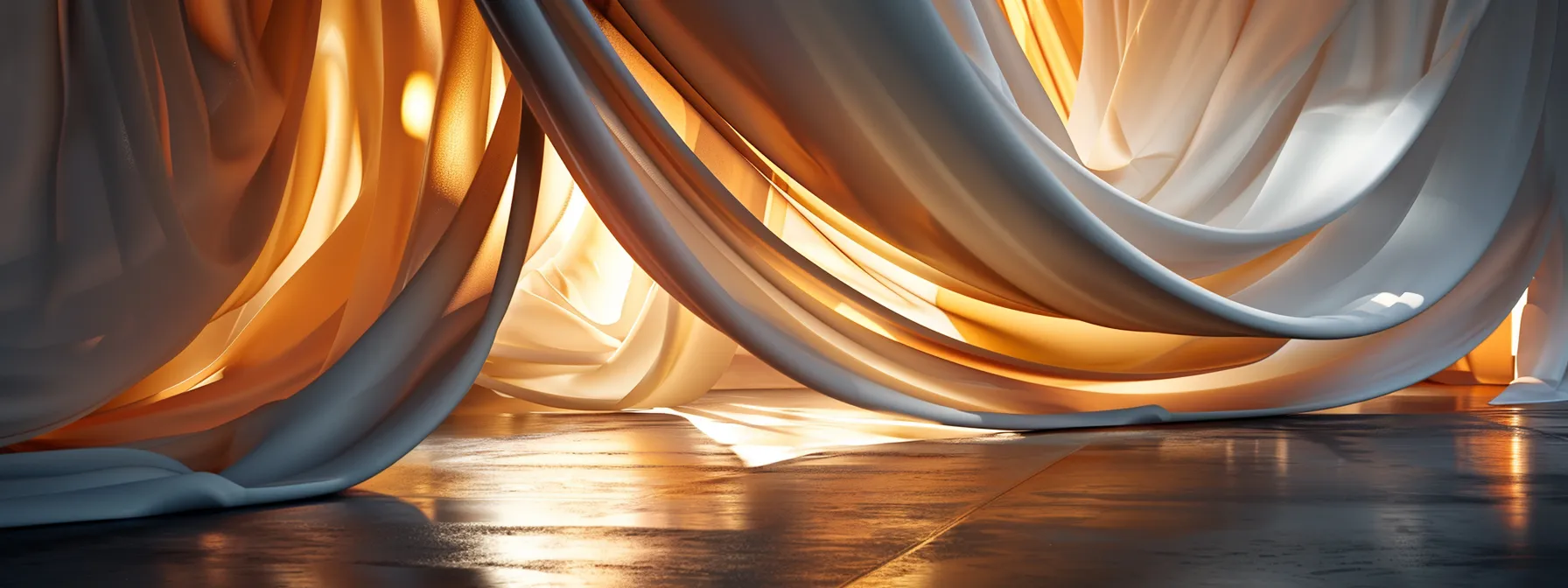
Die effektive Realisierung von Hinterschnitten in Kunststoff-Spritzgussteilen ist eine fortgeschrittene Herausforderung im Produktionsprozess. Die Verwendung von Schiebern und Kernzügen, die Integration von beweglichen Formteilen sowie der Einsatz von lösbar positionierten Kernen eröffnen neue Möglichkeiten, um Zykluszeit zu optimieren und die Komplexität der Teile zu steigern. Diese Techniken ermöglichen die Herstellung anspruchsvoller Produktdesigns, wie solche mit integriertem Gewindeeinsatz oder die Bearbeitung von Teilen durch Fräsen. Sie sind unerlässlich für einen effizienten Produktionsprozess und die Qualität des Endprodukts.
Verwendung Von Schiebern Und Kernzügen
Die Verwendung von Schiebern und Kernzügen ist eine effektive Antwort auf die komplexen Herausforderungen bei der Herstellung von Kunststoff-Spritzgussteilen mit Hinterschnitten. Diese Fertigungsverfahren ermöglichen die Realisierung von Features wie Gewindeeinsätzen in Polycarbonat-Komponenten, die in der Automobilindustrie oder bei der Produktion von Elektronikgehäusen unabdingbar sind. Durch präzises Ein- und Ausfahren der Schieber oder Kernzüge werden Hinterschnitte bei der Extrusion geformt, ohne dabei die strukturelle Integrität der Teile zu beeinträchtigen.
Die praktische Anwendung dieser Technik zeigt sich insbesondere bei Einsätzen von Schraube-Befestigungssystemen. Um in Polycarbonat eine interne Gewindestruktur zu spritzen, nutzen Fertigungstechniker Kernzüge, welche nach dem Spritzvorgang entfernt werden und so die Gewindeform freigeben. Dieser Prozess erfordert ein hohes Maß an Präzision, um sicherzustellen, dass die Teile den hohen Qualitäts- und Funktionsanforderungen in der Automobil– und Elektronikindustrie entsprechen.
Integration Von Beweglichen Formteilen
Die Integration von beweglichen Formteilen in die Konstruktion von Spritzgusswerkzeugen ist eine zentrale Methode, um Hinterschneidungen in Kunststoffteilen zu realisieren. Als Faustregel gilt, dass bewegliche Formteile wie Einschübe oder Kernzüge sorgfältig geplant sein müssen, um die Festigkeit des Werkzeugs und die Langlebigkeit der Spritzgießmaschine nicht zu beeinträchtigen. Aus Aluminium gefertigt, bieten diese Elemente eine Balance aus Festigkeit und Leichtigkeit, um die Dynamik der Werkzeugbewegungen zu unterstützen.
Bei der Realisierung komplexer Teilegeometrien mit Hinterschneidungen ermöglichen diese beweglichen Formelemente eine hohe Präzision und Detailtreue im Endprodukt. Die Konstrukteure bei maxnext.io verstehen es meisterhaft, Aluminium-Einsätze so zu integrieren, dass sie während des Spritzgießzyklus genau positioniert und nachher problemlos zurückgezogen werden können. Dies garantiert eine exakte Umsetzung der Hinterschneidungen und trägt zur Effizienz des Herstellungsprozesses bei.
Einsatz Von Lösbaren Kernen
Der Einsatz von lösbar positionierten Kernen ist eine fortschrittliche Technik im Werkzeugbau für Kunststoff-Spritzgussteile, die präzise Hinterschnitte ermöglicht. Durch den Einsatz von High-Tech Computergesteuerter Fertigung (Computerized Numerical Control – CNC), lassen sich die Kerne so fertigen, dass sie selbst bei hohem Verschleiß noch präzise und zuverlässig aus dem hergestellten Teil entfernt werden können. Derartige Kernsysteme sind oft aus gehärtetem Stahl gefertigt, um der Abnutzung entgegenzuwirken und eine längere Lebensdauer des Werkzeugs zu garantieren.
In der Praxis trägt der gezielte Einsatz lösbaren Kerne entscheidend zur Produktqualität und Effizienz des Spritzgussprozesses bei. Unter Berücksichtigung der Eigenschaften von Stahl und anderer Werkzeugmaterialien optimieren Fertigungsexperten das Design dieser Kerne, um die Zuverlässigkeit der Produktionsvorgänge zu steigern und die Instandhaltungskosten zu minimieren. Diese Maßnahmen sichern eine konsistente Qualität der Spritzgussteile und stärken die Wettbewerbsfähigkeit der Hersteller im Markt.
Einfluss Von Hinterschnitten Auf Werkzeugkosten Und Fertigungszeit
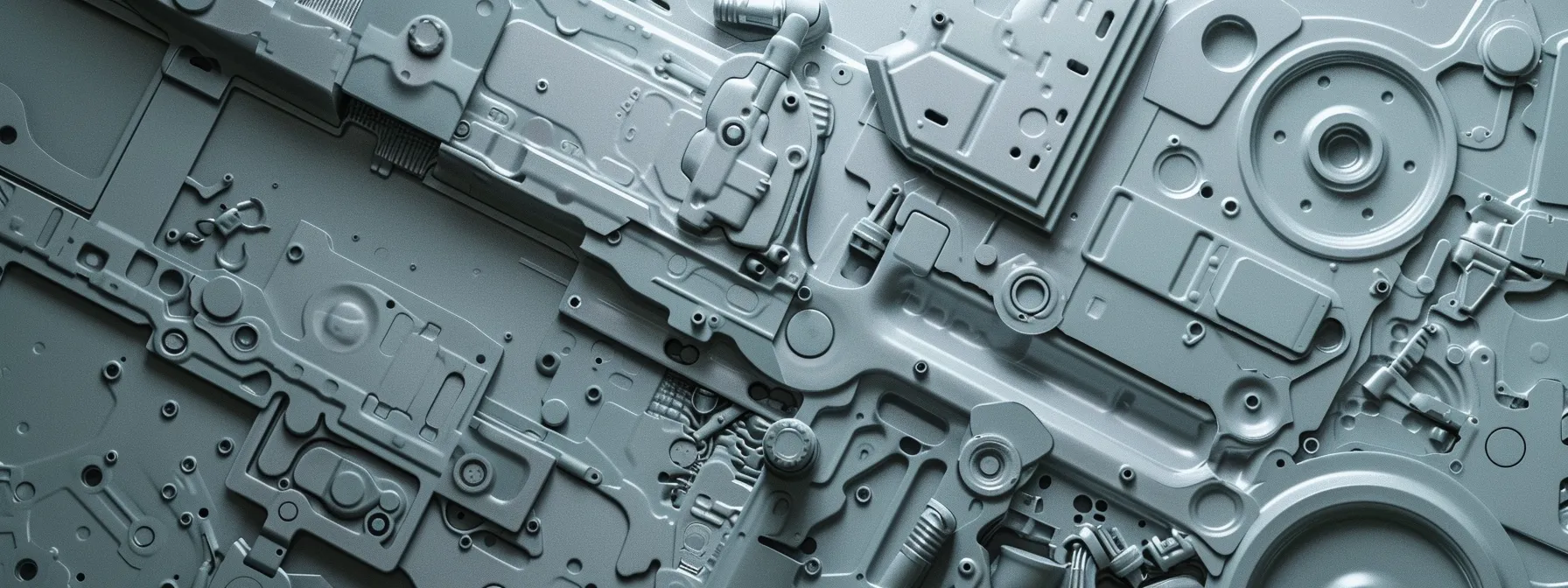
Die präzise Erkennung und Gestaltung von Hinterschnitten bei Kunststoff-Spritzgussteilen ist eine Herausforderung, die sowohl die Komplexität des Werkzeugs erhöhen als auch die Zykluszeiten verlängern kann. Es ist von Bedeutung, wie diese Aspekte bei der Prototyperstellung, Volumenerzeugung und Sicherstellung von Dimensionsstabilität und Elastizität berücksichtigt werden. Darüber hinaus müssen die wärmebedingten Ausdehnungseffekte und ihre wirtschaftlichen Auswirkungen auf den Herstellungsprozess abgewogen werden. Im Folgenden werden die Zusammenhänge zwischen Hinterschnitten, den damit verbundenen Werkzeugkosten und Fertigungszeiten beleuchtet.
Komplexität Des Werkzeugs Erhöhen
Die Konstruktion von Werkzeugen zur Fertigung von Kunststoff-Spritzgussteilen mit Hinterschnitten verlangt nach erhöhter Komplexität, die direkt die Produktivität und das Risiko im Herstellungsprozess beeinflusst. Spezielle Schieber oder Kernzüge, die für die Formgebung von Elastomeren und Silikonen erforderlich sein können, erhöhen den Aufwand in der Werkzeugkonstruktion und bedingen somit eine präzise Analyse und Planung, um Reibung zu vermeiden und die Langlebigkeit der Werkzeuge sicherzustellen.
Dies resultiert nicht nur in höheren initialen Werkzeugkosten, sondern kann auch zu längeren Fertigungszeiten führen, da die komplexen Mechanismen ein sorgfältiges Einrichten und einen korrekten Zyklusablauf benötigen. Ein profundes Verständnis für Materialverhalten, wie das von Silikonen und anderen Elastomeren, ist daher unerlässlich um sicherzustellen, dass sowohl die wirtschaftlichen als auch qualitativen Anforderungen erfüllt werden.
Verlängerte Zykluszeiten Berücksichtigen
Das Schmelzen und der Materialfluss des Kunststoffs während des Spritzgussprozesses sind bei Teilen mit Hinterschnitten oft komplexer und zeitaufwendiger. Faktoren wie der Druck im Werkzeug und die Kühlzeit haben direkten Einfluss auf die Zykluszeit. Durch präzise Simulation können Ingenieure die Produktionsparameter optimieren, müssen jedoch längere Zykluszeiten zur Sicherstellung optimaler Materialfluss– und Abkühlbedingungen einplanen.
Längere Zykluszeiten bedeuten auch eine geringere Gesamtproduktionskapazität, was wiederum die Kosten erhöht. Gerade im Hochleistungsbereich der Kunststoffverarbeitung, wo schnelle Durchlaufzeiten essenziell sind, erfordern Hinterschnitte besondere Aufmerksamkeit in der Planungsphase, um rentabel zu bleiben und gleichzeitig die Qualität des Endproduktes zu gewährleisten.
Wirtschaftliche Aspekte Abwägen
Die Berücksichtigung von Hinterschnitten in der Konstruktion von Spritzgusswerkzeugen kann signifikant in die Werkzeugkosten eingreifen, da eine höhere Präzision vonnöten ist, um Aspekte wie Rauheit und chemische Beständigkeit zu gewährleisten. Eine sorgfältige Abwägung der Werkzeugkonzeption sollte die Langzeitwirkungen wie Verfestigung berücksichtigen, wodurch ein optimales Recycling der Kunststoffe ermöglicht wird, was wiederum die Betriebskosten senken kann.
Des Weiteren beeinflussen Hinterschnitte durch zusätzliche Mechanismen die Fertigungszeit, was die Notwendigkeit präziser Prozesssteuerung unterstreicht, um eine gleichbleibende Qualitätsverarbeitung sicherzustellen. Die Investition in präzisionsfördernde Techniken und Materialien führt zu langlebigen Werkzeugen, was langfristig zu niedrigeren Stückkosten und einer erhöhten chemischen Beständigkeit der Endprodukte beiträgt und somit die Rentabilität steigert.
Best Practices Und Tipps Für Designer Und Ingenieure
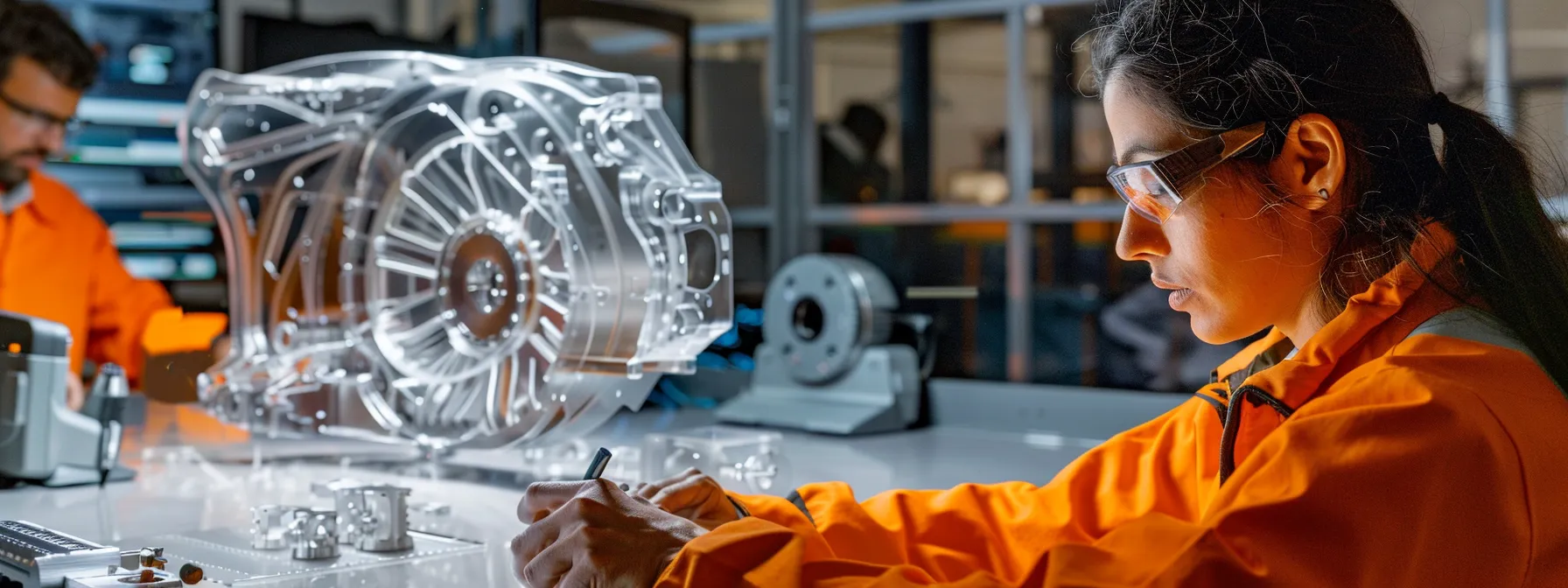
Die Erkennung und Gestaltung von Hinterschnitten erfordert eine fundierte Produktentwicklung, die insbesondere in der Automobilindustrie entscheidend ist. Für Designer und Ingenieure ist die frühe Einbindung des Werkzeugbaus, das Nutzen von Prototyping und Testphasen sowie die Förderung von Weiterbildung und Informationsaustausch unerlässlich. Diese Best Practices tragen dazu bei, Herausforderungen hinsichtlich Mold, Anguss und Durchmesser zu bewältigen und führen zu effizienteren Produktionsprozessen.
Frühe Einbindung Des Werkzeugbaus
Die frühzeitige Einbindung des Werkzeugbaus ist entscheidend, um Design– und Fertigungsprobleme bei Kunststoff-Spritzgussteilen, insbesondere bei der Realisierung von Gewindeformen, zu vermeiden. Ein kollaborativer Ansatz ermöglicht es Unternehmen, Materialkosten zu sparen und gleichzeitig die strukturelle Integrität und die erforderliche Kraft der Teile sicherzustellen. Durch das frühzeitige Erkennen von Hinterschneidungen können kostspielige Nachbearbeitungen reduziert und die Wirtschaftlichkeit des gesamten Projekts verbessert werden.
Fachwissen in der Handhabung von Harz und anderen Kunststoffmaterialien ist für den Werkzeugbau von unschätzbarem Wert, da es das Risiko von Herstellungsfehlern minimiert. Bei der Einbindung der Werkzeughersteller in frühen Phasen können Erfahrungen aus vergangenen Projekten in die Konstruktion einfließen, was zu einer Reduktion von Zeitverlusten durch Iterationen führt und die Effektivität des gesamten Entwicklungsprozesses steigert.
Prototyping Und Testphasen Nutzen
Der Einsatz von Prototyping im Formenbau für Spritzguss stellt eine effektive Methode dar, um hochqualitative Spritzgussteile zu gewährleisten. Durch das frühzeitige Erstellen physischer Modelle können Konstrukteure potenzielle Probleme mit Hinterschnitten erkennen und optimieren, bevor die Fertigung im größeren Maßstab beginnt, was Entwicklungszeit und Kosten senkt.
Zudem ermöglicht das Testen von faserverstärkten Kunststoffteilen in Pilotphasen eine realitätsnahe Bewertung der Produktdesigns hinsichtlich ihrer Funktionalität und Haltbarkeit. Diese Vorgehensweise liefert wertvolle Einsichten für den Formenbau und Spritzguss, die zu einer signifikanten Steigerung der Produktqualität und einer Reduktion von Risiken in der Massenproduktion führen.
Weiterbildung Und Informationsaustausch Fördern
Die permanente Weiterbildung von Designern und Ingenieuren ist für den Fortschritt und die Qualität im Bereich der Kunststoff-Spritzgusstechnologie unerlässlich. Besonders die Auseinandersetzung mit neuen Materialien und Fertigungsverfahren, wie der Implementierung von Hinterschnitten, fördert die Innovationskraft und technische Expertise. Praktische Workshops und Fortbildungen, die aktuelle Herausforderungen und Lösungsansätze vermitteln, stärken das Verständnis für komplexe Teilegeometrien und tragen zur Entwicklung hochwertiger Produkte bei.
Zudem ist ein aktiver Informationsaustausch zwischen den Akteuren der Branche, wie Werkzeugmachern und Kunststoffingenieuren, grundlegend für den technologischen Wandel. Der Austausch über Fachgrenzen hinweg ermöglicht eine tiefere Analyse von Problemstellungen, wie zum Beispiel die Optimierung von Spritzgussformen für Kunststoffteile mit Hinterschnitten. Diese kollaborative Kommunikation unterstützt die Schaffung effizienter Arbeitsabläufe und fördert die branchenweite Standardisierung von Best Practices.
Abschluss
Die Erkennung und präzise Gestaltung von Hinterschnitten ist fundamental für die Herstellung hochwertiger Kunststoff-Spritzgussteile. Sie beeinflusst maßgeblich die Effizienz des Produktionsprozesses, Kosten und die Qualität des Endprodukts. Fortschrittliche Technologien wie 3D-CAD-Modelle und Spritzgusssimulationssoftware sind entscheidend, um Hinterschnitte zu identifizieren und entsprechende Werkzeuganpassungen vorzunehmen. Dieses spezialisierte Wissen ermöglicht Ingenieuren und Designern, die Herausforderungen bei der Fertigung zu meistern und trägt zur Wettbewerbsfähigkeit im Markt bei.