Sheet metal processing online.
- First sheet metal parts in a few days
- Bent parts, cuts, punched and bent parts, formed parts and much more.
- Precise and fast
- Offer in record time all manufacturing processes
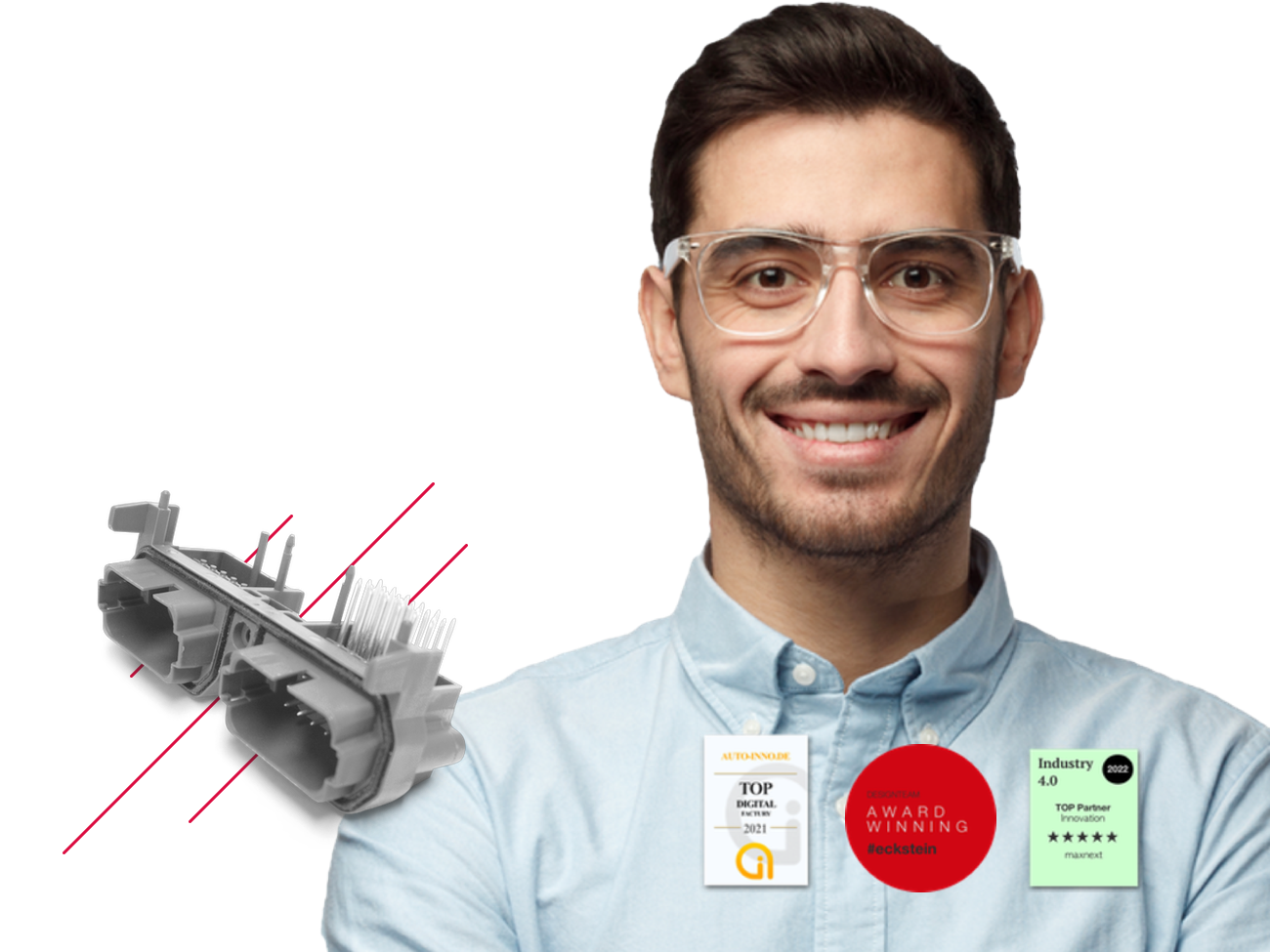
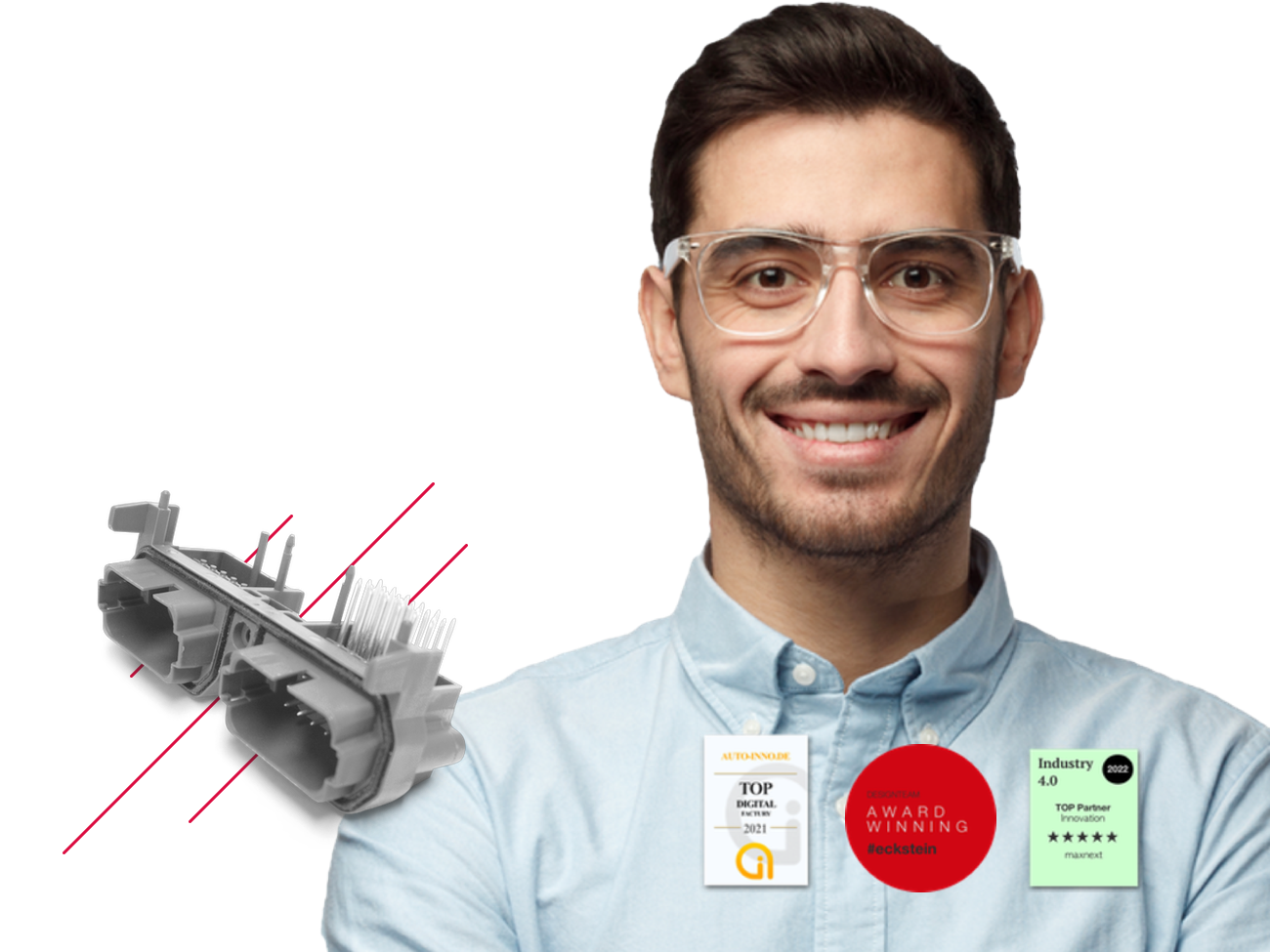
- First sheet metal parts in a few days
- All manufacturing processes
- offer in a few hours
Over 200+ companies
trust maxnext when purchasing
sheet metal parts
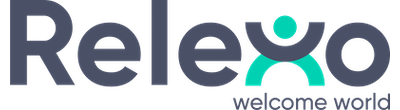
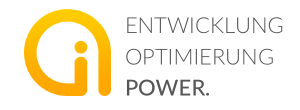
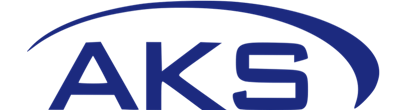
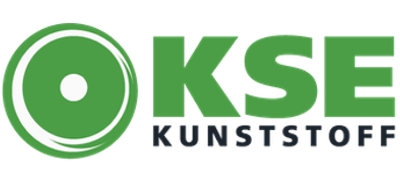
Why maxnext?
The dream of every buyer & entrepreneur. Whether simple components or complex sheet metal parts, fast, personal communication and the best price directly in the first offer.
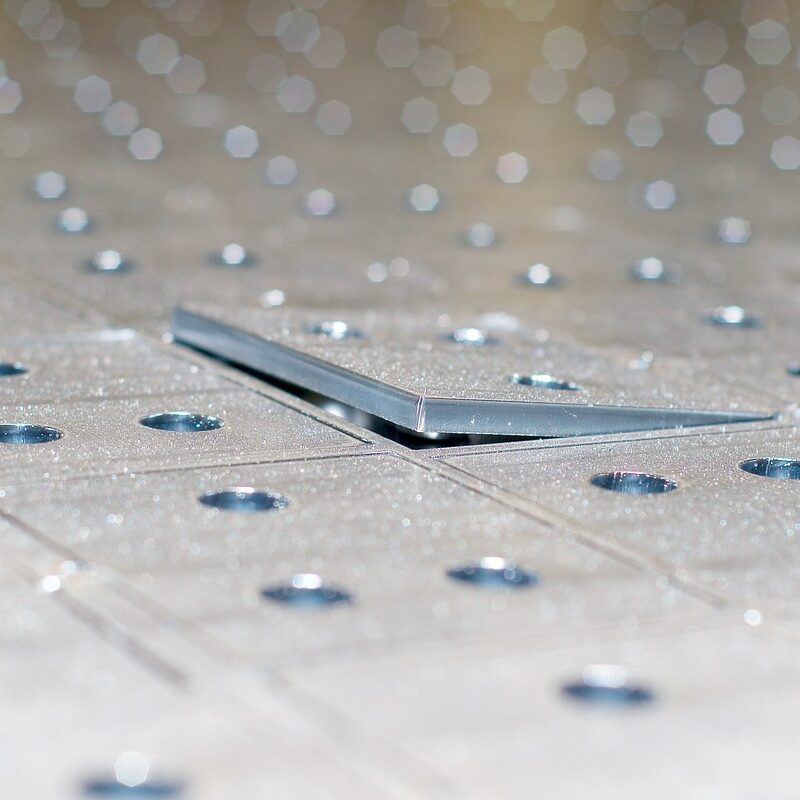
small and large series
Reliable and efficient sheet metal processing online.
Fast & easy to sheet metal parts!
Maxnext is the brand maker of KSE Kunststoff. If you are looking for a reliable and efficient manufacturer of simple or complex sheet metal parts, maxnext is the right place for you.
We find the most economical solution for every project. From development to series production. From simple components to complex assemblies.
Let’s get it started!
“Our goal was to optimize the existing plastic housings of our access points. The result: We are now independent & the purchase has become more economical.”
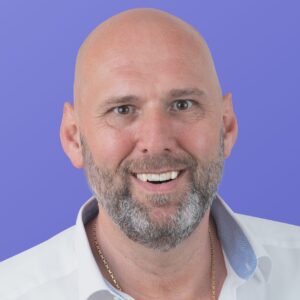
Winfried Zangerle
CEO @ germanhotspot.de
“Quick implementation of our product design. We never thought it would make such an extreme difference to our sales. Thank you!”
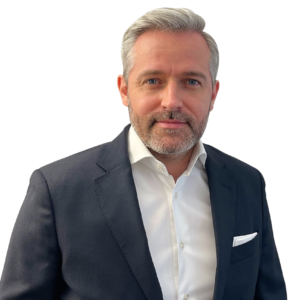
André Becker
CEO @ expertenloft
1000+ successful projects per year!
- Simple and complex sheet metal parts
- The partner for strong brands
- offer in a few hours
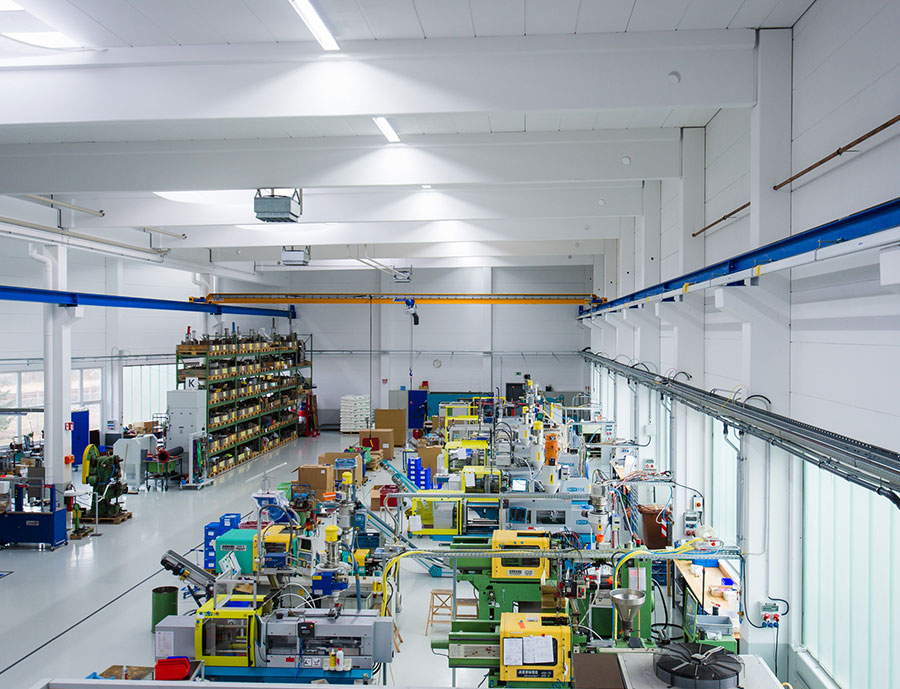
- Cut:
- Cutting For smaller sheet metal parts, lasers or water jet machines can be used to cut the sheet metal to the desired size.
- Cutting with tin snips: For more precise cuts and larger sheets, sheet metal shears are used, which can be operated either manually or mechanically.
- Punching:
- Punching presses: Punching presses are used to produce sheet metal parts with complex shapes and holes. The sheet metal is placed between two moulds and a punch press machine is used to punch out the desired shape.
- Bending and forming:
- Bending: When bending, the sheet metal is bent along a specified line to create angles or edges. This can be done manually with a bending device or mechanically with a press brake.
- Deep drawing: In deep drawing, the sheet metal is placed in a mould and drawn into the mould using a punch to produce complex three-dimensional parts.
- Welding:
- Spot welding: In spot welding, two sheet metal parts are spot-welded together at specific points to create a strong joint.
- Gas-shielded arc welding (MIG/MAG): In gas-shielded arc welding, an arc is created between a wire electrode and the workpiece while a shielding gas is simultaneously emitted to protect the molten metal from oxidation.
- CNC machining:
- CNC milling: In CNC milling, a computer-controlled milling tool is used to remove or add precise shapes and contours from the sheet metal. This process is often used for the production of injection moulding tools.
- CNC turning: In CNC turning, the sheet metal is rotated around an axis while a cutting tool removes the material to produce cylindrical parts.
Precise laser cutting of metal parts and high-quality overmolding with plastic – your solution for tailor-made components!
Our advanced manufacturing process combines high-precision laser cutting of metal parts with first-class plastic overmolding to provide you with customized solutions for your requirements. By using the latest technology and experienced professionals, we guarantee you products of the highest quality and precision.
Why choose us?
Precise laser cutting: Our state-of-the-art laser cutting process enables us to precisely shape metal parts to your exact specifications. Our technology allows us to create even complex designs with the highest precision.
High-quality plastic overmolding: We use only high-quality plastics and the latest injection molding techniques to give your metal parts the properties you want. From material selection to manufacturing, we ensure that your components meet the highest quality standards.
Tailored solutions: We understand that every job is unique, so we work closely with our customers to understand their individual requirements and provide tailored solutions to meet their specific applications.
Reliability and punctuality: We place great importance on reliability and punctuality in delivery. With our efficient manufacturing process and dedicated team, we can ensure that your orders are delivered on time.
Rely on our expertise and experience in laser cutting metal parts and plastic overmolding to meet your needs. Contact us today to learn more about our services and receive a customized quote.
certifications
… we have that too. In our factory near Augsburg we work according to DIN ISO without being certified. That saves money.
Our injection moulding plant near Nuremberg is certified to DIN ISO 9001 & 14001: ideal for anyone who values this.
Frequently Asked Questions
Sure! We know that not all companies have access to 3D data, so we offer a range of 3D data creation services. Email us with your idea and we will design/engineer your product.
It's very simple: Send us your 3D data and we will create a suitable best price offer for you in a short time.
We send the finished parts with a tracking ID. This way you always know where your components are.
In short:
Product development, mold making & manufacturing under one roof. This guarantees short routes. Not only does this save you money, but you are also independent of long and fragile supply chains.
Right across the board: from A for automotive to Z for pet supplies. Whether simple components or complex technical assemblies made from high-performance plastics.
Our extensive and extensive experience from over 25 years guarantees the best results for your project. Request a quote now!
Yes, that is important to us! You will get a personal contact for the production of your parts.
We accompany you in our state-of-the-art CNC machining center from development to series production.